O tema manutenção preventiva em sistemas de baixa tensão é como um mito. Muitos acreditam que seja necessário a realização, mas nunca pensaram em realizar; outros acreditam que não existe a necessidade de uma intervenção, pois o sistema é em baixa tensão e sempre é possível dar um jeitinho caso o sistema venha a falhar.
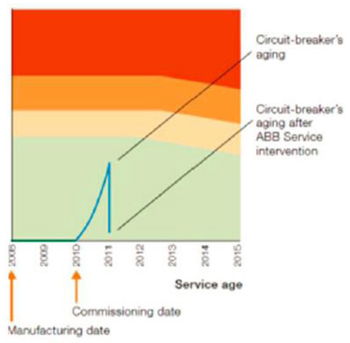
Estes são algumas das respostas que ouvimos de clientes quando mostramos a eles procedimentos e dados de manutenções preventivas. Para simplificar a palavra sistema, vou me atentar para dois produtos: o painel e o disjuntor de baixa tensão.
De acordo com a norma NBR, o termo baixa tensão compreende equipamentos que operem em até 1000 Volts em corrente alternada ou 1.250 Volts em corrente contínua, porém as tensões mais comuns encontradas no Brasil para sistemas industriais são entre 380 Volts e 480 Volts.
Nas muitas visitas realizadas pela equipe de engenharia e manutenção da ABB, encontramos diversos equipamentos que deveriam estar protegendo as instalações elétricas, mas estão empoeirados, com mecanismos com insetos e sistemas de proteção descalibrados e/ou desconfigurados.
A concepção da manutenção nestes equipamentos é apenas estética, que vulgarmente no mundo da manutenção chama-se PLC – Pano Limpeza e Conservação.
A manutenção PLC é feita com um bom produto de limpeza, pano e uma lata de WD (lubrificante). Ou seja depois de tirar a poeira externa do equipamento, as empresas que fazem a manutenção PLC, usam o WD no mecanismo principal acreditando que o mesmo irá assegurar a lubricidade e o prolongamento da vida do equipamento. Duro engano. O WD, depois de três dias, aumenta a retenção de umidade e as partículas suspensas no ar concentram-se com ainda mais rapidez no local onde o produto foi utilizado. Outro fator que chama a atenção é o período da execução. A manutenção deste tipo de empresa normalmente ocorre em 15 minutos por equipamento, pois não existe a preocupação da inspeção das peças, análise de falha, verificação de trincas e análise dos relés. Esta manutenção pode causar em um curto período problemas como:
- Travamento do mecanismo principal
- Não atuação da proteção eletro-mecânica
- Falha de fechamento
- Falha de abertura
A manutenção preventiva da ABB nestes equipamentos tem duração aproximadamente de duas horas, onde o técnico certificado pela fábrica desmonta o disjuntor fazendo a limpeza de todo o mecanismo, analisando possíveis trincas e fissuras das peças. A limpeza de todo o equipamento é executada com um produto biodeagradável que não corrói peças metálicas ou retira a propriedade de lubricidade das graxas especiais que são utilizadas e necessárias para o bom funcionamento do equipamento. Além da limpeza do mecanismo do disjuntor, testes de integridade do relé de proteção, aferição, calibração das proteções elétricas são verificadas pelas ferramentas especiais de manutenção ABB. Como adicional, os sistemas de verificações da ABB geram planos de manutenção baseado nas características de funcionamento do disjuntor. Um algoritmo analisa variáveis como picos de corrente, desarmes pela proteção, quantidades de manobras de abertura e fechamento, além de elaborar o plano de manutenção que através do código de cores possibilita compreender em qual período da vida o produto está e quando sofreu alguma intervenção, auxiliando o cliente na tomada de decisão para novas manutenções ou um processo de substituição que chamamos de retrofit.
Diga não à limpeza PLC e diminua os riscos de uma parada inesperada de seu disjuntor e/ou painel, previna-se com a tecnologia e serviços ABB.
Mecanismo usando o WD
Mecanismo com limpeza ABB
Gráfico de ciclo de vida do produto ABB
Marcel Serafim - Gerente de Serviços de Produtos de Baixa Tensão
Sobre a ABB:
ABB (www.abb.com) é líder em tecnologias de energia e automação que permitem aos clientes de concessionárias, indústrias, e transporte e infraestrutura melhorarem o desempenho, ao mesmo tempo em que reduzem o impacto ambiental. O Grupo ABB de empresas opera em cerca de 100 países e emprega aproximadamente 145.000 pessoas.